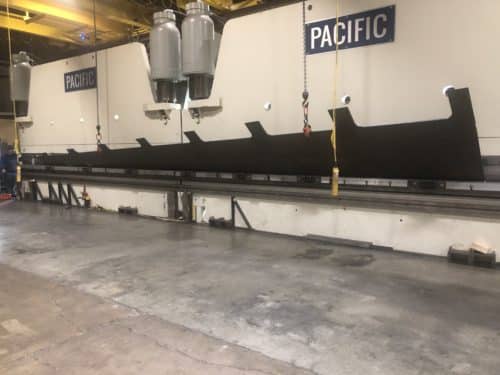
Since 1905, the team at G.E. Mathis Company has dedicated itself to quality, integrity, and craftsmanship. We continue to grow our expertise in metal fabrication, combining our talented staff with advanced equipment to deliver high-performance components per your unique specifications and application requirements.
Press brake forming is just one of our extensive metal fabrication service offerings. We utilize various techniques to maintain high levels of quality and accuracy while providing fast turn times and cost-effective solutions. Learn more about the benefits of our custom press brake forming services, methods and applications, and the G.E. Mathis Company difference.
Advantages of Precision Press Brake Forming
You’ll benefit in numerous ways from our press brake forming services, experiencing the following:
Our equipment can achieve tight tolerances, delivering components per your exact specifications every time.
With inexpensive tooling and decreased material waste, precision press brake forming can be a cost-effective option for your business.
Press brake forming is compatible with everything from prototyping to high-volume manufacturing, allowing us to scale our operations based on your needs.
Incorporating automation into our press brake forming processes adds a high level of accuracy and speed to our operations, boosting productivity and shortening lead times compared to manual processes.
In comparison with progressive dies, the multi-station tooling involved in press brake forming can achieve more complex part configurations. We can make adjustments based on your required part thickness, dimensions, angles, and more.
Understanding the Different Types of Press Brake Forming Options
Depending on your requirements, we’ll use the optimal press brake forming method for your project. We offer:
An ideal solution for enclosures or structural applications, the G.E. Mathis Company team uses this technique to form highly accurate channels and U-shaped components with reliable angle and leg length consistency.
For optimal project versatility, we utilize coining to generate sharp, tight-tolerance bends whereas we’ll use air bending for broader applications for which softer radius bends are preferable.
By reproducing punch radii, our forming equipment is capable of creating reliably repeatable bends through bottom bending. Whatever your design specifications, we can form the necessary radius bends for your project.
By folding the edges of a metal sheet over, we can enhance the strength of your component while achieving a smooth finish for a pleasing, polished aesthetic.
We can generate complex bends and angles as well as unique part configurations with precision using angular bends and multi-axis forming.
Industries We Serve
Our team serves a diverse client base, with customers in the following markets:
- Agriculture
- Architecture
- Chemical
- Construction/cranes
- Defense
- Energy
- Marine
- Mining
- Transportation
- Trailers/truck bodies
Contact Our Experts for Custom Metal Forming Solutions
At G.E. Mathis Company, we’re committed to providing customers with industry-best precision metal forming solutions. Our advanced equipment, extensive experience, and dedication to quality continually meet the demands of a broad range of industries and applications.
Contact us to learn more about our precision brake forming capabilities, or request a quote today.
Request Quote
Please complete the form below and we will contact you shortly.
Over 100+ Years of Experience
Trained & Certified Expertise
Reliable Customer Service